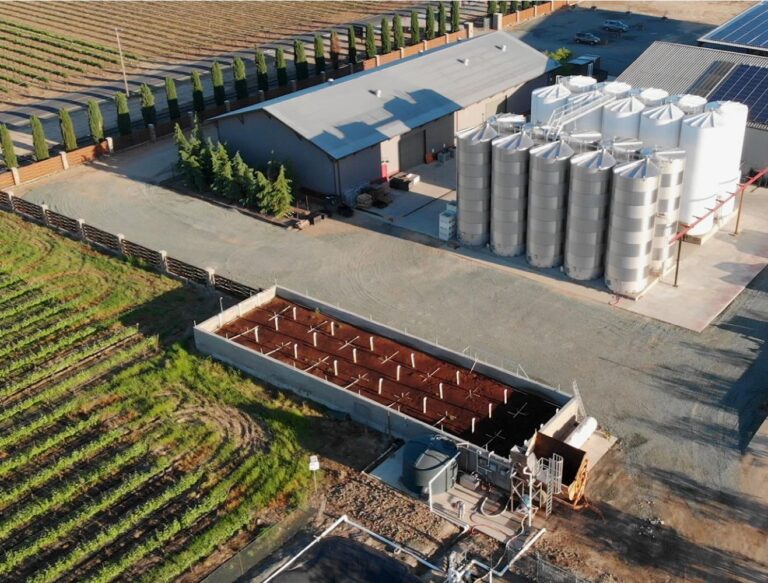
For years, Peltier Winery and Vineyards near Acampo, California, relied on an aeration pond to treat wastewater coming from its operation. At times, odors emanating from the pond weren’t compatible with the nearby tasting room.
After learning about the BioFiltro Biodynamic Aerobic, or BIDA, system at the Unified Wine Symposium, winery owner Rodney Schatz thought long and hard before pulling the trigger in 2017 to have one installed on his winery. The patented vermifiltration process harnesses worms and beneficial microbes to remove biochemical oxygen demand (BOD), total suspended solids (TSS) and total nitrogen from wastewater.
Since Peltier installed the system, the odors have all but disappeared, the system proved simple to operate, and the worms have become a source of pride shown off during Earth Day and other events.
“It’s my favorite thing to talk about; what do worms have to do with wine?” said Faryn Schatz, Peltier marketing manager, whose father installed the system. “Farmers are very practical people, and they’ll only do something that will actually work. This does work. It saves money on energy, it doesn’t smell as bad as the wastewater pond and the water is cleaner in four hours compared to two weeks. It works, just as simple as that.”
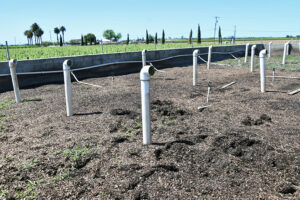
The worm-based systems have caught the attention of other wineries as well as other food processors and food waste handlers. During a recent industry tour of Peltier Winery, Bogle Family Vineyards Assistant Winemaker Mckensie Smith was asking questions and taking notes. Although the Clarksburg-based winery has currently put expansion on hold, she said she was doing research for potential long-term growth.
“Bogle trumps ourselves as being as sustainable as we can,” Smith said. “We’re always willing to trial new things at Bogle.”
Worms Catching On
To date, Davis-based BioFiltro has completed more than 30 vermifiltration systems with additional ones under construction in the United States, said Sarah Haupt, sales engineer. Most are at wineries, although several large Western dairy installations are currently in the works.
Rated for peak flows of 10,000 gallons per day, the 3,000-square-foot Peltier Winery installation is considered midsized. Similar to package wastewater treatment plants, BioFiltro has self-contained systems built using 20-foot-long shipping containers for boutique wineries and other small operations.
On the other end of the spectrum are larger systems. In 2016, Fetzer Vineyards in Hopland was the first winery to install a BioFiltro BIDA system. With a 100,000-gallon-per-day peak capacity, it comprises 21,000 square feet of worm beds. And a 5-acre system at O’Neill Vintners & Distillers in Parlier is designed to handle up to 1 million gallons of wastewater per day.
In addition to being a winery with the associated winery wastewater, O’Neill also is a distiller. With that process comes additional BOD and TSS from cooking and distilling the grain base, Haupt said.
In a one-pass system like Peltier uses, the vermifiltration system removes 80% or more BOD and TSS and 50% or more total nitrogen, Haupt said. Because the Acampo operation already had a pond, it uses it for final polishing of the treated water before applying it to vineyards for irrigation.
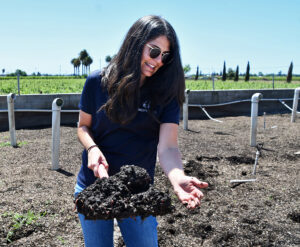
In Napa and Sonoma counties, on the other hand, she said wineries may use a double-pass system because the water is going directly into the drip irrigation system. There, the outflow from the worm beds is recirculated for additional treatment, which altogether removes 90% to 95% BOD and TSS.
Customized Systems
Although each system is designed and engineered specifically for an individual operation, Haupt said they all follow some basic concepts. Each project is sized to handle peak wastewater production.
Once the appropriate-sized area is excavated, an impermeable liner is installed along with concrete walls. Then comes a layer of pallets, screening, a layer of gravel, more screening and then 3 to 4 feet of biomass, whether wood chips, other low-value woody material or corn stover. The design allows for passive oxygenation of the system.
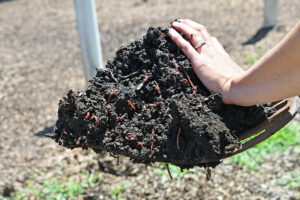
At Peltier Winery, wastewater flows from floor drains and through a screen or another type of filter to remove large particulate matter before moving into an equalization tank. There, buffers are added to reduce the typically acidic winery wastewater to a pH of about 6.5.
Over the years, Haupt said, they found beneficial microbes in the worm beds will raise up the pH from 6.5 to a neutral 7.0.
From there, the buffered wastewater will move to a holding pit or tank for eventual application. The system is low-energy, since most of it is gravity-fed, she said. This compares to aeration ponds, which are more energy-intensive because they need to be agitated around the clock.
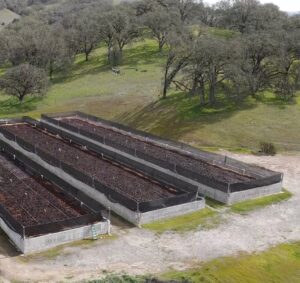
A programmable logic controller, or PLC, automatically turns off and on the sprinkler system. Proper moisture levels are key, and the system typically irrigates about once every 30 minutes.
With food processors that only run a few months out of the year, Haupt said they recommend continuing to irrigate during the off season to keep the worms going.
Although they won’t have as much food, she said the worms compensate with reduced reproduction.
Once the filter substrate is established, the system is inoculated with worms from a similar nearby system.
BioFiltro uses Eisenia andrei, a red wiggler species closely related to the common vermicomposting worm, E. fetida. Both are epigeic, meaning they prefer compost, leaf litter or manure-related environments to mineral soils.
BioFiltro technicians help owners get the system running and stabilized, which takes about three months. Then the company offers several maintenance and operation options. System owners can take over the system themselves or they can pay the company to do it.
“If the client wants to take over operations, then they can,” Haupt said. “You don’t need high tech. Peltier does it 100% themselves.”
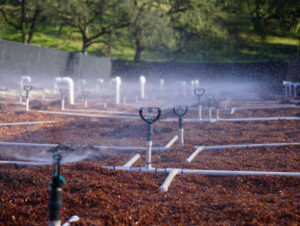
Low-Tech Maintenance
Depending on the amount of water being treated, maintenance typically involves tilling the top layer of the worm beds roughly monthly to break up any crust or solids that may have formed.
Because of the smaller size, Peltier has a worker complete the task. But larger operations have developed automatic tilling systems that run up and down the worm beds.
Haupt said she also encourages system owners to routinely check for clogged sprinkler heads or sensors that might need recalibration.
Every two to three years, owners need to replace the filter beds as the organic substrate has decomposed past its useful life. To do this, she said, they first set aside a portion of the material that includes worms for eventual re-inoculation. Think of it like saving starter culture for sourdough bread.
Using an earth excavator, the owner digs out the remaining substrate material, which can be used as vermicompost for on-field application or sold. In Peltier’s case, they apply it to their vineyards to enhance soil organic matter.
Once the new 3- to 4-foot filter bed has been installed, the material is inoculated with the saved worm cultures and the process begins anew about three to four weeks later. In wineries and other seasonal food processors, this is typically done in the offseason.