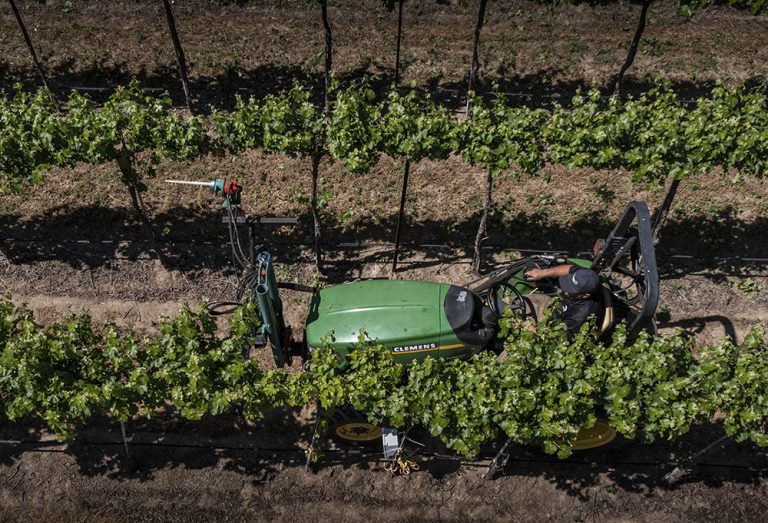
Prompted by labor availability and ever-increasing labor costs, winegrape growers have increasingly turned to mechanization, first with harvest and then with other cultural practices.
The move didn’t come overnight and has been more of an evolution, said S. Kaan Kurtural, founder of Kurtural Vineyard Consulting in Davis, Calif. In addition, a fully mechanized production system isn’t for every grower, and they must weigh their production practices before making the jump.
But Kurtural has proven it can be done, whether growers are planting a new vineyard or wanting to convert over an older one.
For more than 20 years, he has studied mechanized winegrape production first at California State University, Fresno, and then at UC Davis, until earlier this year. One of the most recent projects he led was establishing a “touch-free” experimental winegrape vineyard at the UC Davis Oakville Station.
“15 years ago, there wasn’t a lot of economic necessity to do mechanized practices,” Kurtural said. “However, grape prices have not changed in the last 25 years. Now it’s become a necessity, and there’s been a change in the ways vineyards are planted and farmed.”
Controlling labor costs has become a focus as state minimum wages increase annually. That’s because labor tied to pruning and harvesting account for more than 80% of overall vineyard labor costs, according to research conducted by Kurtural and several colleagues.
George Zhuang, UCCE viticulture advisor in Fresno County, conducted four studies in 2019 that estimated the costs and returns of establishing and producing winegrapes in the southern San Joaquin Valley. The research, which looked at nearly complete mechanization, involved four varieties: cabernet sauvignon, chardonnay, rubired and colombard.
Based on the studies, fully implemented mechanization reduced production costs from $3,000 to $2,500 per acre, or 17% less.
Because the studies were completed four years ago, Zhuang said he couldn’t help but expect the savings to be even more today with the state’s annual increase in minimum wage.
“If you still use my numbers, the savings have jumped from $500 to at least $700,” he said.
Aiding the transition are the growing number of U.S. equipment manufacturers that have developed machines to box prune vines in one pass, Kurtural said. Many European machines, on the other hand, are designed more for the VSP (vertical shoot-positioning) trellis system and only prune on one plain.
Trellising is Key
Choosing the proper trellising that provides 360-degree machine access without cross arms or wires getting in the way is key to making full mechanization successful, Kurtural said.
Other factors to consider include topography, cultivars, rootstocks, vine and row spacing, irrigation systems, climate and yield potential. Cultivars that can be trained to have straight trunks and lateral cordons lend themselves to mechanized management. In addition, those with strong basal bud fruitfulness, such as chardonnay and cabernet, are better suited to mechanized management than varieties like Thompson seedless with lower basal bud fruitfulness.
In several trials, the single high wire trellis system performed the best, reducing labor costs by more than 90% and increasing fruit yields without reducing quality. Known by other names, including high-cordon machine pruned, the system involves training bilateral cordons on a single wire about 60 to 72 inches off the vineyard floor. Canes are allowed to flow over the sides to create a kind of parasol over the fruiting zone. The leaves don’t totally block the sun, instead acting like a sun screen to filter rays that hit the fruit.
The single-wire system isn’t far removed from the California sprawl, where bilateral cordons are topped by a single catch-wire, and canes are allowed to sprawl over the sides to create a canopy covering the fruiting zone. Where the single-wire system differs is it lacks extraneous wires that may interfere with mechanical pruning blades, saws or sickles.
The single-wire system also elevates fruit higher off the vineyard floor, minimizing damage from spring frosts that are colder closer to the ground. Recent UC research led by Kurtural also has found the system protects fruit from heat waves or increasing temperatures by keeping it farther away from heat radiating from the vineyard floor.
The VSP system, on the other hand, uses a fruiting wire about 36 to 40 inches from the ground. Three to five additional movable wires allow for shoot training. The fruit is exposed to the sun, making it prone to sunburn. The lower fruiting wire also makes buds and new leaves more susceptible to spring frosts.
While the California sprawl system works for mechanization, cross arms with two catch wires can cause big problems for mechanical pruning or shoot thinning.
In addition, the single-wire system typically helps balance canopy size with fruit load without affecting grape quality. In fact, Kurtural said, the new systems actually enhance desirable chemical components such as anthocyanins within the fruit.
“We initially started work to see if [full mechanization] would be economically profitable for the grower,” he said. “Once we established that, we noticed that the quality was much higher at the farm gate. In the end, the wine was preferred by taste panels as well.”
Mechanical Pruning
Along with harvest, dormant pruning is one of the most labor-intensive and costly cultural practices tied to winegrape production, according to Kurtural’s research.
Over the years, he and his colleagues have found that mechanized box pruning, where bearing spurs are pruned from the top, bottom and sides, mostly closely resembles hand pruning. The initial prepruning pass leaves a box with dimensions ranging from about 4 to 6 inches wide and about 4 inches tall.
Because mechanical pruning is not selective, follow-up mechanical shoot thinning after bud break and the danger of frost has passed helps achieve the desired shoot density.
Making the Switch
Zhuang, who cooperated with Kurtural in some of his previous trials, said nearly all new vineyards being planted in the south San Joaquin Valley are on single high-wire trellises.
“It’s very obvious right now based on my observations that all of the new plantings of winegrapes are on single wire or high quads shooting for 100% mechanical pruning,” Zhuang said.
Because yield is the top goal of south San Joaquin Valley producers, he said shoot thinning and leaf removal aren’t that popular.
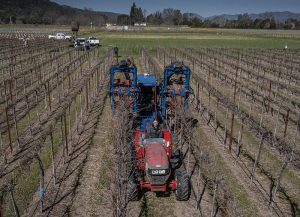
Zhuang was part of research with Kurtural in 2019 that examined the feasibility of converting a hand-pruned San Joaquin Valley vineyard to mechanization. The 20-year-old head-trained merlot vineyard was planted on traditional trellising that involved two eight-node canes laid on a catch wire in opposite directions and two eight-node canes attached to a 66-inch-high catch wire. Although the system could be mechanically harvested, it didn’t lend itself to mechanical dormant pruning or shoot removal.
As part of the trial in the Madera vineyard, they converted 8 acres of vines to a cordon-trained spur-pruned California sprawl system or a bilateral cordon-trained mechanically box-pruned single high wire system. Of the two, the single high wire proved more successful for mechanical pruning in the San Joaquin Valley, where more than half the state’s winegrapes are grown.
Retraining the vines also resulted in yields and fruit quality as good or better than from hand-pruned vines. Once the project was completed, the vineyard owner converted the remaining 45 acres of vines to the single high-wire system.
But Zhuang said there is a caveat when converting vines to a new trellis system.
“We see a lot of those old vineyards in the south San Joaquin Valley have a lot of trunk disease, so there’s a lot of dead arms,” he said. “Typically, we don’t recommend growers convert those vines because diseases like Botryosphaeria and Eutypa will come back and impact your new vines.”
But if the vineyard is relatively healthy without a lot of dead arms, Zhuang said it would be a good candidate for conversion.